How to produce Perfect Plastic ?
Memorial University Scientists say carbon dioxide has the solution.
Devastating effects of plastic on Environment
The damage to the environment by plastic use needs to be
controlled.The biggest problem with this is that once they have been soiled the
end up in the trash, which then ends up in the landfill or burned. Either
solution is very poor for the environment. Burning emits toxic gases that harm
the atmosphere and increase the level of VOCs in the air while landfills hold
them indefinitely as part of the plastic waste problem throughout the globe.

Marine debris that was washed ashore covers a beach on
Laysan
Island in the Hawaiian Islands National Wildlife Refuge.
It has been estimated that one bag has the potential to unintentionally kill one animal per every three months due to unintentional digestion or inhalation. If you consider the number of littered plastic bags ranges from 1.5 million to 3 million depending on location, this equals a lot of ecosystem sustaining lives lost.

Burning of plastic
Without the balance of the ecosystem food sources dry up and starvation occurs. With an increase in plastic bag use throughout the world, the eventual effects could be literally devastating even to the human population.
How MUN researchers are working toward a biodegradable plastic.
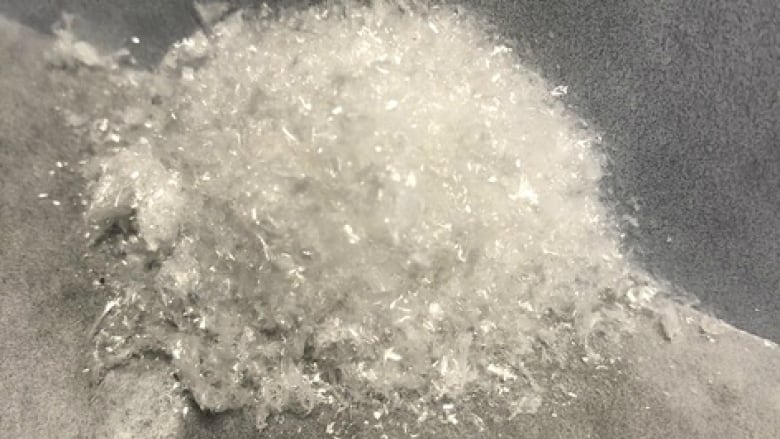
This purified polymer could be cast into a film used to make an
environmentally friendly alternative to plastic bags.
environmentally friendly alternative to plastic bags.
With the provincial government continuing its research on the possibility of banning single-use plastic bags, graduate students in chemistry at Memorial University are researching new materials that would make bags biodegradable.
Kori Andrea says it would likely be difficult to ban plastics altogether, but she's part of a team of researchers working to create a better, more environmentally friendly alternative that would break down at the end of its life.
Andrea said she's using the carbon dioxide abundant in the environment as the basis for new biodegradable materials.
"What we're looking at is being able to take carbon dioxide and actually use it as a starting material in these polymers or plastics that we're making," she said.
"We're taking carbon dioxide, we're reacting it with another starting material called epoxides, and then making these alternating polycarbonates, and these are your plastics."
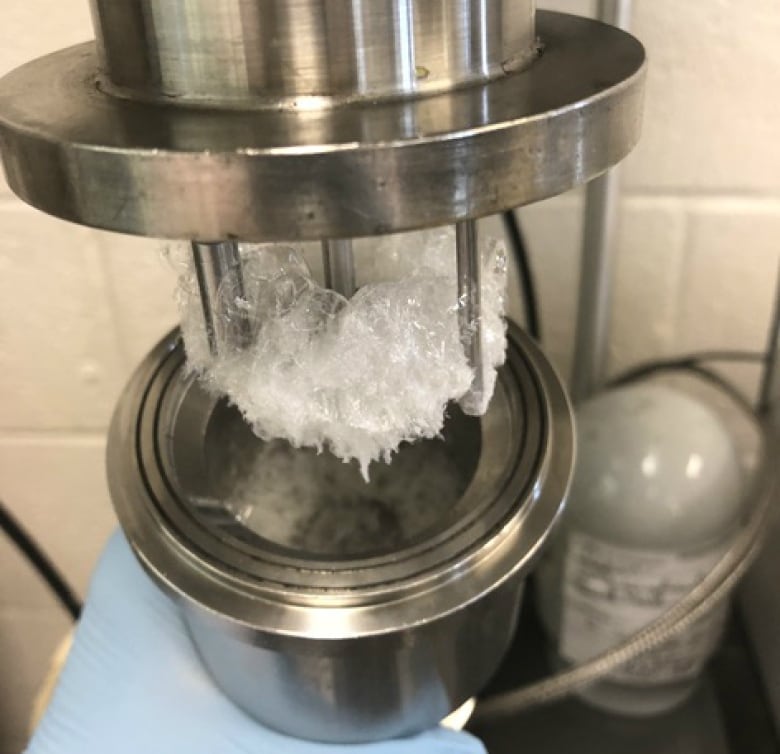
yield this material. Some trapped carbon dioxide can be seen
in bubbles. (Kori Andrea/Submitted)
Andrea said many plastic materials now in use are made from
petroleum products, which are built with carbon-hydrogen bonds and don't easily
decompose.
"It's hard to break down because if you think of the organisms and bacteria in the environment today, they don't have to break down bonds like that, so of course, everything bio-accumulates over time," she said.
"With incorporating carbonate linkages, these carbon-oxygen bonds in our materials, there are bacteria out there that are capable of breaking these things down."
Modifying materials
It's a case of "Mother Nature knows best," Andrea said, using raw materials that fit with natural processes.
Andrea said some of these biodegradable plastic-like materials are already being made by companies in the United States and the United Kingdom, but they have drawbacks.
She said she and other researchers at MUN are modifying the materials they are making to make them more heat-resistant for things like lids for paper coffee cups, or to have different densities to mimic different pre-existing materials.
"We're looking at taking our materials and alternating them one way or another — can we make something similar to a plastic wrap that's very flexible? Can we make something similar to what milk jugs are made of that's a bit more durable?" said Andrea.
"We have recently found some different ways to modify them and start to really change their melting points or their durability. We are getting there. We're still at the fundamental stage and the development on the lab scale."
Scaling up
The challenge now, she said, is to make these products on a large scale with existing technologies and equipment.
Andrea said high pressure is needed to make the carbon dioxide react, so she's designing catalysts to make those reactions occur without high pressures or temperatures.
But it's hard to know what the end products will cost until they are scaled up to produce larger quantities.
"Can we make them? Yes. Can we make them cheaper than the processes that have been optimised for 50-plus years? I don't think we're there yet," she said.
"But will we get there? I think we definitely will."
Is it not cool that Carbon dioxide, a commonly known hazardous gas can be used to balance ecosystem ?
Comment below and share your thoughts.
Reference: https://bit.ly/2TnBfxC